Reinventing Baltimore’s Waterfront
October 21, 2024

This article was originally published in the March/April 2004 issue of DEMOLITION magazine.
Sitting at the epicenter of the original 13 colonies and possessing a protected deepwater port, colonial Baltimore naturally developed as a hub for commerce. Location was likewise integral to future economic development. Shipping was far cheaper overland or rail transportation. The Port of Baltimore was the United States’ closest major port to her heavy industrialized Midwest with its auto factories and steel mills. The presence of a port, with its purpose of accepting raw materials, including cheap labor from all over the world, and of exporting finished products sold to other nations, made the city and economical location for manufacturing. Steel, automobiles, soaps and detergents, appliances, garments, armaments and even beer were produced and shipped from Baltimore.
During the 1800s, Baltimore became a major point of entry for German immigrants. Large German neighborhoods took root, and with them a thirst for their native lager-style beer. This style of beer would become the dominant style enjoyed by the American public.
Established in 1885, the National Brewing Company, the largest of Baltimore’s 22 breweries, would grow to produce over 1 million barrels of beer per year. Over 900 people drawn from the sea of row houses of east Baltimore were employed at the height of production.
In 1933, the local Hoffberger family acquired the National Brewing Company. They would subsequently own the Baltimore Orioles and Crown Central Petroleum Corporation. These entities were well entrenched in the minds of all Baltimoreans by their constant presence at all Oriole games. A local advertising agency, W.B. Donner, rose to national prominence with their conception of an official mascot for National Brewery, “Mr. Boh,” and the award-winning “Land of Pleasant Living” campaign.
The economic principles that gave rise to Baltimore’s prominence were also significant in its decline. The deregulation of the trucking and freight railroad industries in the 1970s turned the Port of Baltimore’s inland location into a distinct disadvantage. It was now cheaper to move materials overland, making Atlantic ports such as those in the Tidewater Virginia region more advantageous.
Simultaneously, many third-world countries were beginning to industrialize. Extremely cheap labor, coupled with other low costs of production and little government regulation, initiated a drastic transformation of the world economy. A considerable portion of the manufacturing of consumable goods left the United States.
The advent of the information age, while beneficial to the American economy as a whole, proved detrimental to America’s older, industrial cities. Location was no longer as significant as in the past. Talent and capital could now be defused. Proximity to customers was achieved electronically. This left much of the former plant structure vacant, rotting and producing no job opportunities or tax revenue. The modestly educated masses who had clustered within walking distance of their former employers now found themselves far from the economic action.
Location, coupled with the vision of two Baltimore entrepreneurs, would usher in another resurgence of economic development. Baltimore possessed over 14 miles of waterfront property, most of it occupied by defunct industrial enterprises. William and Fred Struever, as well as some other Baltimore developers, saw the hidden value in many of these architecturally significant structures. They felt they lent identity to and created differentiation from other cities. Their developments created frenzied peripheral economic development. The city once again was becoming the hot destination for the young, talented and creative to live.
The former National Brewery sitting atop one of the highest elevations in Baltimore City, with commanding views of the Port of Baltimore, the trendy Inner Harbor and its downtown high rises, the Johns Hopkins Hospital and university complexes, and virtually every residence in east Baltimore caught the eye of these two savvy developers.
The project to transform this former beer manufacturing facility into a $100 million economic focal point was put out to bid. Following hundreds of hours of walkthroughs and estimating, the demolition segment of the project was awarded to Baltimore’s premier demolition concern NDA member The Berg Corporation.
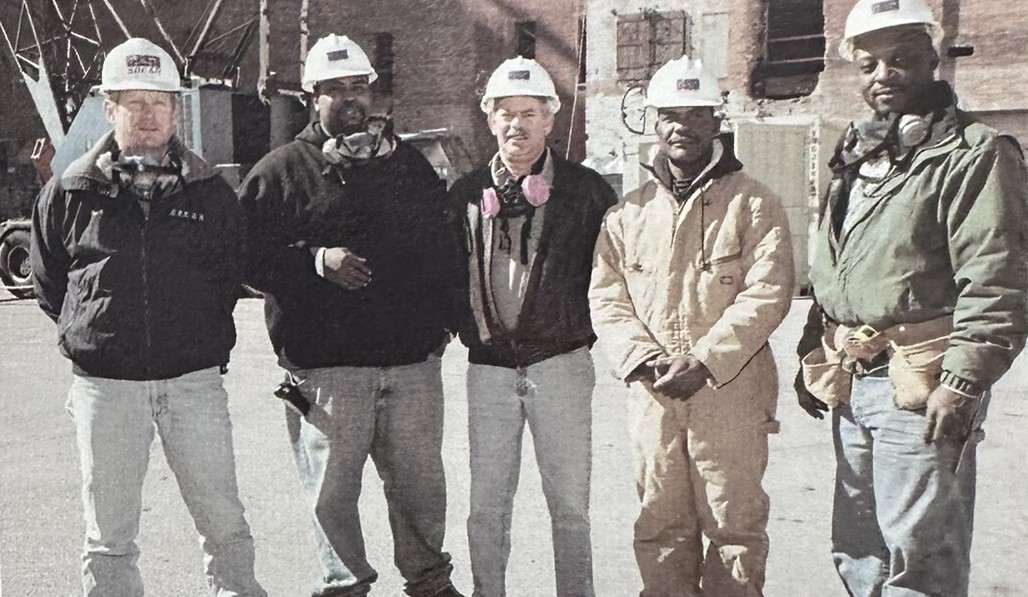
Now that the high fives were over, it was time to begin planning for the gutting of this 200,000-square-foot, severely lead-contaminated structure. Compliance Environmental, an environmental consulting and testing firm, was contracted for consultation and to develop a formal plan to properly and safely work in this unique environment. They worked hand in hand with The Berg Corporation during the entire planning of the project. The two firms met at Berg’s office for a formal review of drawings and scope. A site meeting was held to walk every inch of the structure so compliance could further review the idiosyncrasies of the project. They also attended the pre-construction meeting to fully understand the concerns of the client. The first draft of the lead plan was scrutinized point by point by all parties, and adjustments were made.
Following the pre-demolition meeting, the work plan was reviewed and revised four additional times. The final version was extremely detailed and covered required documentation, testing requirements, means and methods, proper engineering controls, site-specific safety equipment to be utilized, containment requirements, proper clothing and personal protective measures, and decontamination procedures prior to vacating the containment area.
Separate English and Spanish versions of lead-in-construction training were held at The Berg Corporation’s offices, with all of their subcontractors required to attend. Consultants were brought in from 3M Corporation to suggest proper respiratory protection. Two separate gas and air companies were invited to demonstrate and price out 49,000-degree plasma cutters. Berg utilized the services of two environmental subcontractors with burning capabilities to assist them in the removal of eighty 40’ x 12’ x 12’ glass-lined, lead-painted fermenting tanks. They had one month to remove all of them.
Berg employed two of their top superintendents to manage this project. One would work outside the building, overseeing all documentation required under the lead plan and the paperwork generated through haul-off, gas and air deliveries, daily work sheets, and time cards. He also oversaw crane and backhoe operations, general housekeeping, the ordering of supplies, coordination with waterproofing environmental subs, toolbox talks and general safety matters, and acted as liaison with the general contractor’s chief superintendent.
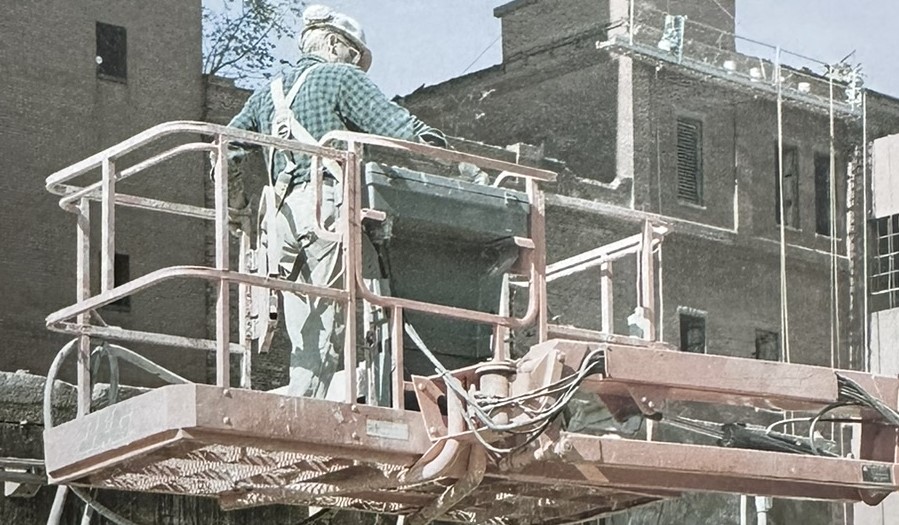
The second superintendent worked exclusively inside the building, overseeing compliance to the lead plan and ensuring safe, productive work practices by their in-house labor as well as Berg’s subcontractors.
There were three distinct commodities to be removed from the site. A light, cork-type insulation would be transported 40 cubic yard containers to a per ton construction/demolition type landfill. A local recycled shipped 40 cubic yard containers of ferrous steel. Birck walls and concrete slabs were transported by tandem axel dump trucks to a secondary site to be crushed and reused. Berg staged a Hitachi EX 200 to facilitate loading. They utilized their 80-ton P&H crane to offload steel and cork coming out of the building. The crane was made available to their client and its subs to get material on and off the structure.
The complexity and safety concerns of the job necessitated an especially close working relationship with the general contractor, SBER. Daily discussions helped to clarify and focus attention on executing the safety plan. The spirit of cooperation that developed was a fantastic source of innovation and ideas that helped to keep the project on schedule, profitable and safe.
The project posed certain procedural challenges. Asbestos abatement and mercury decontamination were taking place simultaneously with demolition activities. At times, Berg was delayed from progressing to the next work area as they waited for these specialty trades to complete their work. Architects were involved in a work in progress, constantly changing scope during the course of the project. Access to the building by upper management was curtailed by the Byzantine requirements of the lead plan. In addition, the project had an extremely aggressive schedule.
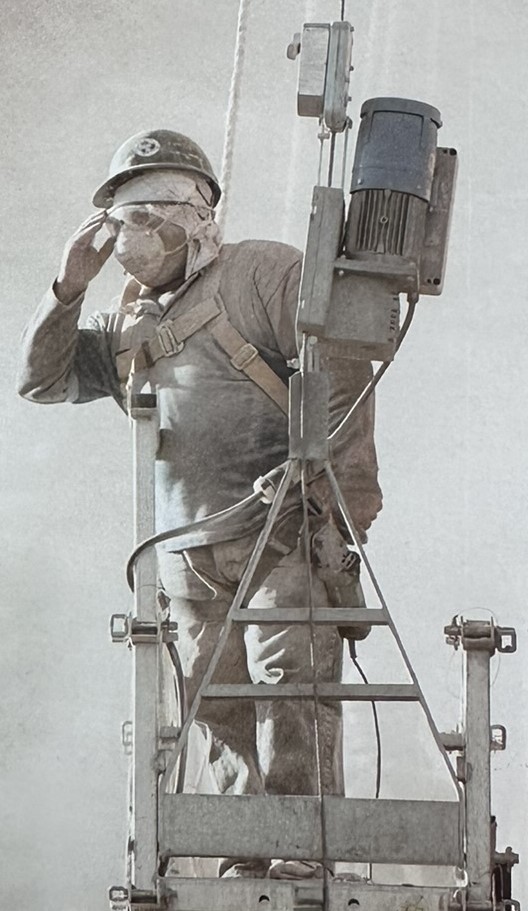
An 80-ton crane, swing stages, scaffolding, 60 employees, lead-in-construction and burning glass-lined, lead-painted tanks, not exactly the scenario you would like to see a Maryland OSH (MOSH) inspection to take place. For two weeks, as Berg worked on this complex project, two MOSH inspectors were a constant presence.
They reviewed every page of Berg’s general safety plan, site-specific lead plan and Hazard Communication Program. They read all the documentation generated by the requirements of the lead plan (benchmark blood lead testing, subsequent blood lead testing, lead in construction certification cards).
They inspected Berg’s crane and all yearly inspection documentation. Inspected gauges, torches and all burning apparatus. Checked fall protection security features, swing stages, bobcats and backhoes. Monitored adjacent properties for any contamination originating from our project. Scrutinized respirators for proper application and condition. Conducted random air sampling. The result of all this scrutiny? No serious violations.
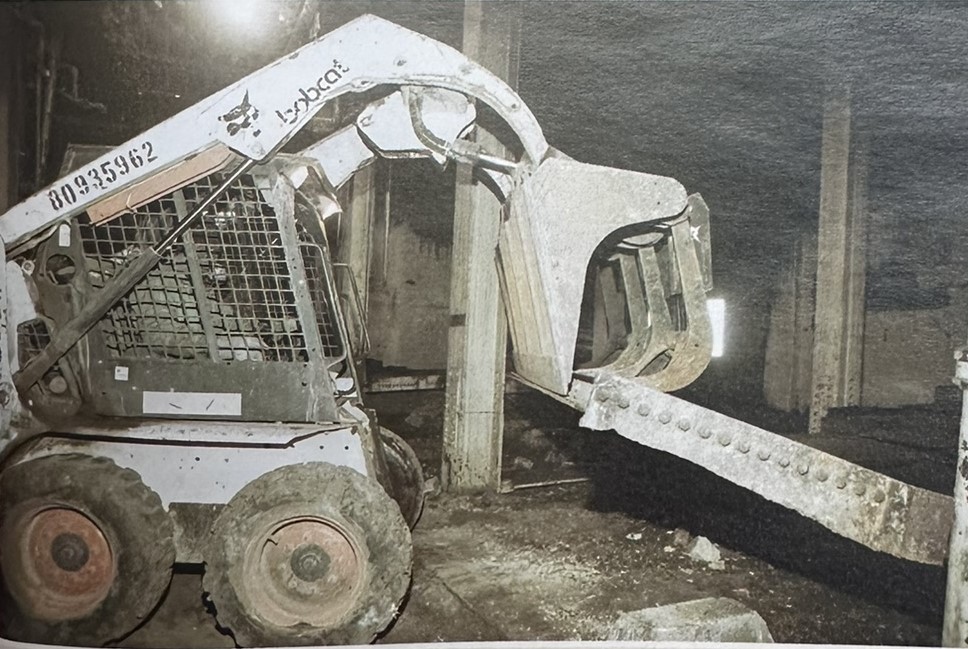
This project, while being one of the most complex and unique jobs Berb ever tackled, also became one of their most successful. The key was proactive planning and execution. The Berg Corporation hit the ground running. They began negotiations with vendors immediately. Training classes were scheduled the day they were awarded the job.
Berg scrutinized their lead plan, scope and drawings with their subcontractors. They walked the site with all the appropriate parties to further ensure a complete understanding of procedures. Project progress and adherence to procedures were reviewed on a daily basis. This provided the venue to reiterate all pertinent safety procedures on a daily basis.
The Berg Corporation was able to complete this extremely complex environmental abatement and demolition project on time and on budget, a tribute to superior planning and talented supervision.